The materials we use to make products are usually chosen with performance as the highest priority, followed by cost. Performance encompasses both as-manufactured parameters and long-term reliability. While these metrics are crucial, they are not the only concern. Increasingly, environmental impact plays a more significant role in materials development and selection. There is talk of “sustainable materials.” This is more than just a fad.
The phrase “sustainable materials” is meaningless without context. Here are a few relevant strategies:
- Improve product designs to require less raw material,
- Substitute less energy-intensive materials,
- Replace toxic compounds with nontoxic alternatives,
- Develop new materials to replace conventional ones,
- Improve recycling infrastructure and processes.
Let’s examine this through the lens of semiconductor packaging. Several factors affect whether a material qualifies as “sustainable.” We need to consider the environmental and social impacts of material production, how material choice affects yield and reliability, and whether the supposed benefits outweigh the drawbacks.
Product Design
For decades, our industry has been shrinking design rules to pack more functionality into a smaller footprint. We typically do this to improve performance, not to reduce the consumption of raw materials. Regardless, the result is often greater capability per gram of materials used.
One side effect of design shrinks is increased concern about thermal management. High-power integrated circuits (ICs) packed densely generate a lot of heat. Printed circuit boards (PCBs) can incorporate thermal vias and optimize traces to improve heat dissipation, but heat sinks are often still required.
The higher the thermal conductivity of the heat sink material, the smaller it can be while providing enough heat dissipation. Diamond is an extreme example of a high-conductivity material that can be used to make heat sinks. However, given the human rights violations associated with diamond mining and the high energy required to produce synthetic diamond, copper or another metal alloy might be a better option for sustainability.
Energy Consumption
The energy required to produce a ton of material varies by several orders of magnitude, from 2.5 Gigajoules (GJ) for lumber to 53,000 GJ for gold. Many materials our industry relies on are energy-intensive, and there are often no readily available substitutes.
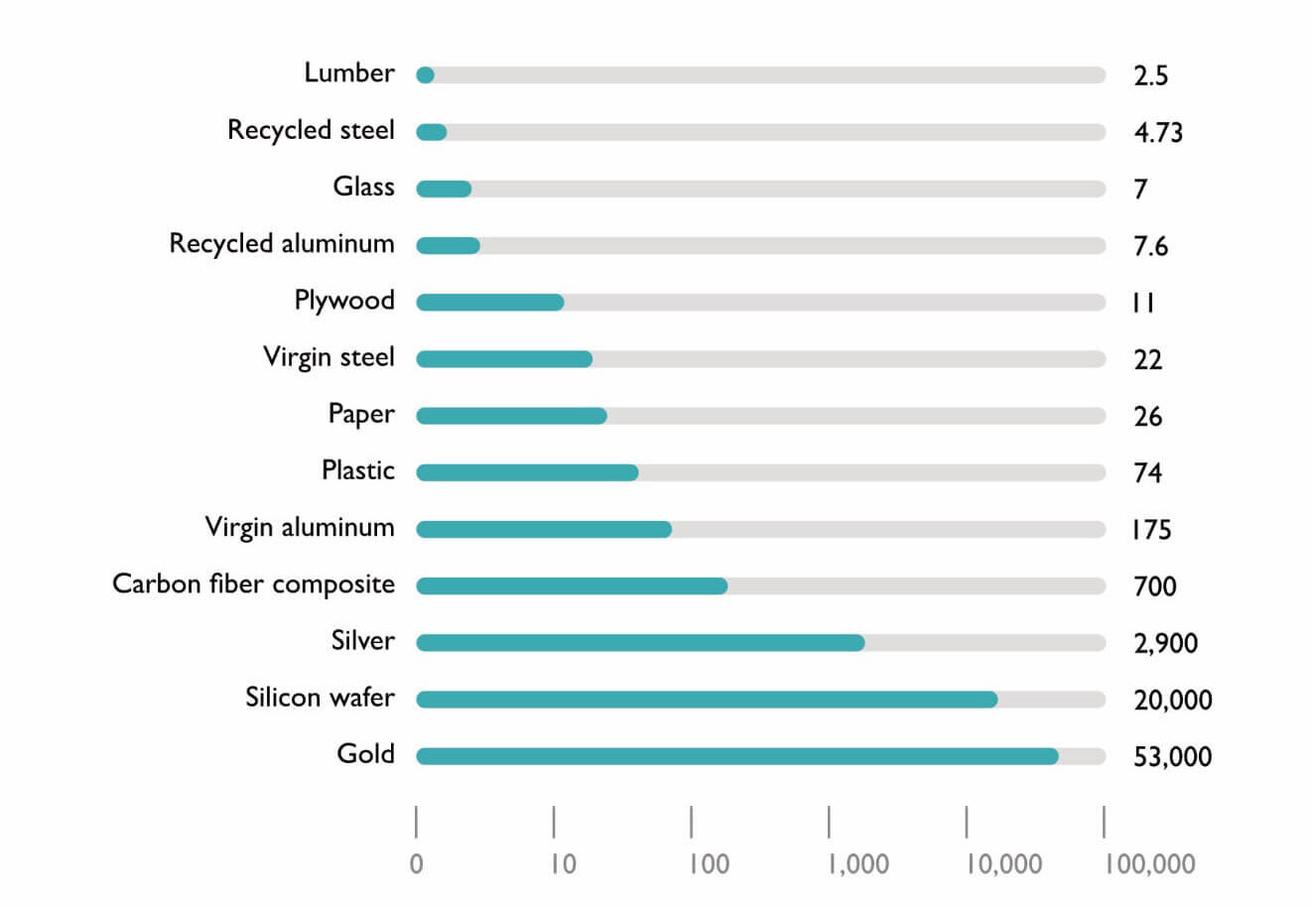
That said, the performance of a given material often outweighs the energy cost, especially considering the amount of material required. Switching to a material with higher electrical conductivity, thermal conductivity, or strength can allow designers to use less of it to achieve the same result. The most direct energy-per-ton benefit comes from switching from virgin to recycled metal. More on that below.
The energy source used to produce materials and make them into products is also important. Powering facilities and equipment throughout the supply chain from renewable energy should be a high priority.
Material selection also affects energy consumption by allowing processing at a lower temperature or for less time.
For example, incorporating lower melting solders saves energy during reflow. Unfortunately, the transition to lead-free SAC solders 20 years ago increased the melting point. Indium Corporation has developed reliable lead-free solder alloys that contain indium (no surprise there) and bring the melting point back toward that of eutectic tin-lead.
Another application where energy savings are possible is the temporary bonding and debonding of thinned wafers during wafer-level packaging. PulseForge won a 3D InCites Technology Enablement Award in 2024 for its photonic debonding technique. The process applies high-intensity light pulses and operates at room temperature. It offers high throughput without heating the entire wafer or requiring harsh chemicals.
Toward Biodegradable Circuit Boards
In traditional product packaging, biodegradable or compostable containers are gaining acceptance. What about semiconductor packaging applications? Is a biodegradable printed circuit board (PCB) possible?
Not entirely, as it contains metal traces, but some layers could be biodegradable. For example, plant-based fibers can theoretically replace epoxy resins, as some have a suitable dielectric constant. These materials have the added benefit of being nontoxic. Plant-based PCBs are not yet a commercially viable product, but researchers have shown proof of concept and produced functional boards.
The idea of biodegradable PCBs is interesting, and reducing toxicity is especially compelling. Realistically, though, this solution has problems. Biodegradable boards will likely not be able to withstand typical metal deposition and etching processes or conventional reflow oven temperatures. It is possible to replace subtractive metallization with additive processes and switch to low-temperature solders. Still, the likelihood of biodegradable PCBs getting to industrial composting facilities is low. We have a hard enough time collecting and processing e-waste as it is.
Improving Recycling
Metals are among the most easily recycled raw materials. They can generally be melted, purified, and reused repeatedly without losing quality. Recycling expensive metals such as copper, silver, and gold reduces the greenhouse gas emissions associated with their production and can be economically worthwhile.
Things are more complicated when it comes to metals used in semiconductor packaging. There are two issues: 1. the difficulty in extracting the metals from the rest of the assembly, and 2. the reliability of wire bonds, flip chip bumps, or solder joints made from recycled metal.
Multiple organic and inorganic materials need to be separated, at considerable expense, to recover individual metals. The purity and microscopic grain structure of the resulting metals are crucial to product performance. Processes that work to extract metals for less stringent applications may not be good enough.
That said, making highly reliable wires from recycled metals is possible. TANAKA Precious Metals offers bonding wire and electroplating compounds made from recycled gold. At present, these are niche products, but the hope is an industry where 100% recycled precious metals content is standard practice.
Your Turn
As you look at the examples above, what strategies look applicable? What measures could your company take to choose more sustainable materials?