Without a global supply chain, many of the microelectronics industry’s innovations wouldn’t have come to fruition. Although we often talk about the technical aspects of the advanced packaging industry at 3D InCites, at the end of the day, we need access to equipment to create the packages of the future. Transporting large and expensive semiconductor equipment is no easy task – it requires intense logistical and risk mitigation planning, highly-specialized personnel, and several other considerations you may have never thought about.
To understand what it really takes to move equipment from one end of the world to the other, I spoke with experts from Kuehne+Nagel who shed light on the details of mitigating semiconductor supply chain risks when shipping the industry’s complex and highly calibrated tools.
Routing and Security Considerations
Because many semiconductor manufacturing tools require specialized carriers to accommodate their size and temperature needs, getting them from point A to point B can quickly become difficult and expensive. In addition, companies must also be mindful of how often a piece of equipment is physically handled during its end-to-end journey. Barry O’Dowd, Global Head of Business Development Semicon at Kuehne+Nagel, noted that any time equipment is handled, it runs the risk of being damaged.
But choosing a route that’s as cost effective and direct as possible is only a small piece of the shipping puzzle, it is about identifying and dealing with risks. Security can be another major concern. For instance, if high-value semiconductor equipment or indeed chips need to be stored in an airline warehouse, a logistics expert must determine the best course of action for keeping the chips safe from damage or theft. O’Dowd mentioned that if the airport doesn’t have a high-value storage cage, one way to mitigate this would be to hire a security guard to monitor it there. Strategies like this can help companies avoid costly re-routes or loss and damage-related delays.
“The value of equipment is high, and the value of damage could be even higher,” said O’Dowd. “If that equipment is essential for opening a production line, those delays could be massive for a business that has invested heavily for that.”
Risk Management Basics
O’Dowd also underscored the importance of logistical risk management when shipping semiconductor tools. To manage risk, all parties involved in the shipping process must be informed and unified on which actions to take and when.
When I asked how Kuehne+Nagel manages each facet of the shipping operation, O’Dowd pointed to the importance of conducting lane risk assessments. In logistics management, a lane is the term for a route that’s commonly taken between two cities. To ensure a tool gets across each lane successfully, the lane must be equipped to handle the transport that’s required. This is taken care of by origin offices that manage the trucking companies, prepare the freight, and organize flights.
However, when a company ships a tool to the other side of the world, the order of people and processes can quickly become complex. Language barriers must be addressed, schedules should be thoroughly managed, and appropriate precautions must be taken. But out of everything I learned, what surprised me the most was how logistics companies sometimes need a say in the creation process of the tools themselves. As the tools become larger, tool designers need to ensure they’re creating machines that can be shipped on time.
“The size of the machines are getting bigger,” said John Desmond, Vice President of Semiconductor at Kuehne+Nagel. “When they hit the market and we’re asked to ship them, we have to try to unpack their requirements. Logistics experts should be involved in the planning of shipment preparation, which is an important step because you may need to develop new sensors or a new methodology for monitoring these shipments.”
With everything to consider, O’Dowd highlighted how important it is to unify the logistics chain and assess the risks at each step. He explained how Kuehne+Nagel achieves this through its Risk Mitigator software solution. Stakeholders input data at each point to generate a risk score, the software color-codes it, then Kuehne+Nagel investigates each risk to develop appropriate mitigation strategies (figure 1).
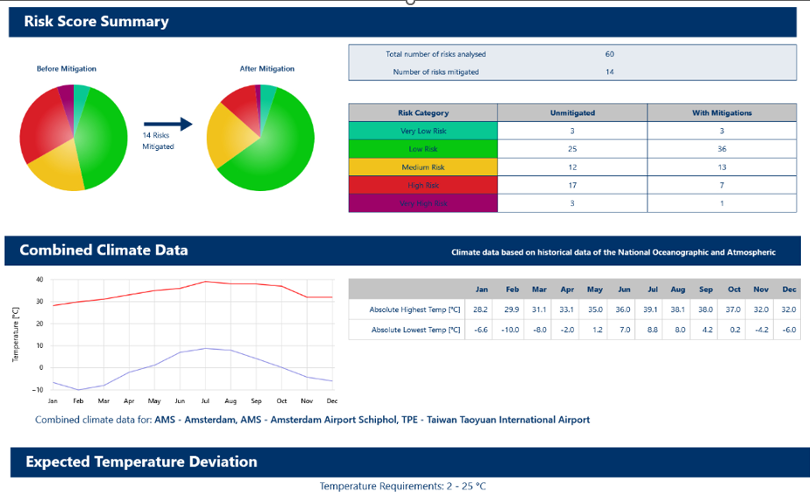
“[Risk Mitigator] has Kuehne+Nagel at the beginning point and the end point, so we’re the controller of this,” said O’Dowd. “We give stakeholders access, and based on that login, they get individual instructions they have to follow for the shipments they’re responsible for.”
As helpful as it is to organize the logistics process, I had to ask – what happens when a stakeholder doesn’t comply with data entry? O’Dowd mentioned that if someone doesn’t comply, that logistics partner will become “a critical risk.”
“For example, if the airline isn’t entering [data], then we have to find a new airline,” said O’Dowd. “That airline made itself too risky to use, because they’re not providing the information that enables us to understand how to deal with everything in the appropriate way.”
To learn more, join us for a dynamic live panel discussion moderated by 3D InCites Françoise von Trapp and featuring sustainability expert, Julia Freer, and industry leaders from Kuehne+Nagel, ABM, and YES, as they share practical strategies for navigating current challenges—and preparing for what’s next. This isn’t just a conversation. It’s a roadmap to turning risk into resilience and sustainability into a competitive edge. Registration is free!