When the United States and Europe looked to re-shore semiconductor technology, the primary focus was restoring leading-edge manufacturing and creating more resilient supply chains throughout the ecosystem. Eventually, it emerged that nearly all of the leading-edge advanced packaging took place in Asia, and there was minimal packaging capability in either the US or Europe.
This should not come as a surprise to anyone involved in the industry. Almost as soon as the semiconductor industry started manufacturing chips; test, assembly, and packaging were moved offshore, as it was considered more economical to perform those tasks overseas. This trend led to strong growth of outsourced semiconductor assembly and test service (OSATS) providers and integrated device manufacturer (IDM) packaging across the Asia Pacific (AP) region.
The Asia Times wrote that advanced packaging is the next front in the chip wars. If you think that conquest or success in war arises from how much territory, or in this case manufacturing is performed in Asia, then this will be a long-drawn-out battle where the Asia Pacific region already has most of the territory. When the U.S. Department of Commerce (DOC) was preparing the arguments for the CHIPS Act, it was determined that only 3% of the packaging occurred in the U.S., and of that very little advanced packaging when the report was first written.
While the USA is attempting to recover some of that packaging share, the real hotspot for packaging is in the Asia Pacific Region. The market can be broken up into the semiconductor fabs that also do advanced packaging either for themselves or foundry partners and the OSAT companies, which are essentially the packaging and test foundries for the majority of the industry. SEMI is tracking over 500 OSAT providers and 170 IDM facilities. As the graph shows the majority of these packaging facilities are in the Asia Pacific Region.
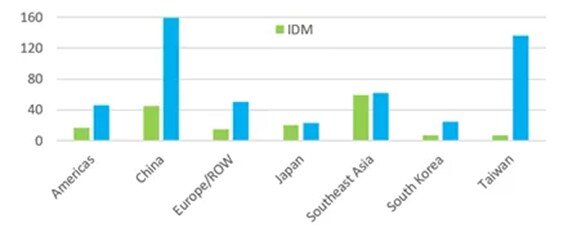
Companies manufacturing chips, both IDM and foundry, provide a considerable amount of packaging services in the AP region. The foundry operations of Samsung and TSMC have significant packaging capacity and are adding more as demand for chiplets to support AI capacity for their partners. Chiplets are also finding their way into phones, automotive, and PCs, which is increasing the demand for chiplet capacity to which the OSATS are responding in partnership with fabs and foundries.
Samsung, Hynix, and Micron perform most of their memory packaging in the AP region. Samsung and Hynix are packaging mostly in Korea with some manufacturing occurring in China. Micron has facilities in Singapore, Malaysia, China, and Taiwan. Micron is also expanding to India with a new facility expected to open in 2025. Intel has packaging and assembly facilities in Malaysia, China, and Vietnam in addition to its US efforts.
OSATS makes up the bulk of the packaging resources for the semiconductor industry. Most of these facilities are located in the AP region, with China and Taiwan having over half of the OSAT facilities and revenue across the industry. According to IDC, the top 10 OSAT companies are responsible for over 80% of the industry’s revenue, with ASE and Amkor, the top 2 OSAT companies, accounting for over 40% market share. The top 10 OSATS are located primarily in Taiwan and China, with one in Singapore. The OSATS have facilities spread throughout the AP region, for example, Amkor has packaging facilities in Taiwan, China, Korea, Japan, Malaysia, Vietnam, and the Philippines.
- ASE Group: Headquarters Taiwan
- Amkor: Headquarters USA, Manufacturing mostly AP
- Powertech Technology Inc: Headquarters Taiwan
- Chipmos Technologies: Headquarters Taiwan
- King Yuan Electronics Co. Ltd: Headquarters Taiwan
- Formosa Advanced Technologies: Headquarters Taiwan
- JCET: Headquarters China
- UTAC Holdings Ltd: Headquarters Singapore
- Lingsen Precision Industries Ltd: Headquarters Taiwan
- Tongfu Microelectronics Co.: Headquarters China
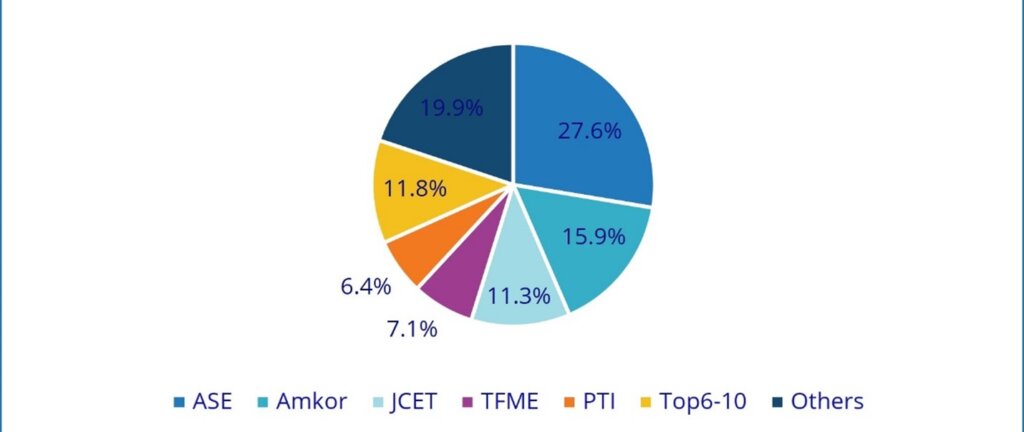
With all of the chiplet noise in the marketplace, one might think that most of the chiplet development occurs either at TSMC in Taiwan or at Intel in the U.S. This is far from the case. A considerable amount of chiplet devices are assembled and packaged at the OSATS. AMD has partnered with Tongfu Micro to handle its chiplet packaging. Tongfu and AMD co-developed their chiplet capability in 2017 when AMD first started chiplet development. Intel’s Embedded Multi-die Interconnect Bridge (EMIB) packaging, which is considered 2.5D, is done in Malaysia as well. Foveros is packaged in the US at the moment, but that may also be outsourced to AP.
Samsung has a considerable 3D packaging effort for its advanced logic foundry partners, Samsung Advanced Logic, and HBM located in Korea. SK Hynix performs most of its HBM packaging and development in Korea as well. All the memory companies are partnering with TSMC, or other OSATS to get their HBM integrated into advanced packages.
OSATS are a big part of the 3D ecosystem, an most packaging development happens at these companies. ASE has long partnered with TSMC and got a shout-out at TSMC’s North America OIP presentations. Amkor is also moving forward with TSMC in Arizona for 3D packaging technology.
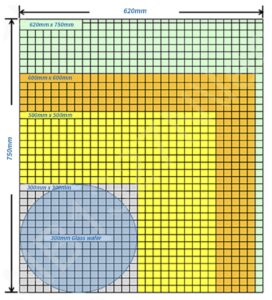
Panel-level packaging (PLP) is a hot new technology for chiplet manufacturing. Wafer-level packaging (WLP) cannot support the volume of chiplet devices needed by the microelectronics industry. The industry is shifting from using wafers or round substrates to glass panels. Innolux in Taiwan is operating a 3.5G panel-level packaging plant. TSMC just purchased a 5.5G flat panel factory for the same purpose and Micron has been looking at several flat panel facilities for PLP. TSMC expects to have a 9-reticle package in production by 2027.
Advanced packaging will continue to be an area of strong growth for the industry. In a recent earnings call, CC Wei, CEO of TSMC, mentioned that in 2023, the foundry business was about 117 billion dollars; however, with the addition of advanced packaging to TSMC’s and other companies’ product lines, the foundry business was estimated to be 250 billion dollars. That’s a doubling of the foundry market and is mostly due to advanced packaging.
With a market size of over 100 billion dollars and no signs of the AP region slowing down in the packaging market, AP will continue to be the hot spot for advanced packaging for some time to come.
This article first appeared in the 2025 Yearhook. Read the full issue here.