As the world demands faster and smarter technologies than ever before, the importance of underfill is gaining traction in the realm of advanced packaging. Underfill is an epoxy that helps fill gaps between a chip and its substrate. It’s important because it works to relieve stress on the chip, thus making the chip more reliable.
Although there are many different types of underfill, I sat down with Jack Melton from NAMICS to tap into his expertise in liquid mold underfill. From my interview, I learned that one of its biggest advantages is its single-step process of overmold and underfill. Because of this, liquid mold underfill has the advantage of speed.
If you’re wondering, overmold is exactly what it sounds like. It protects and insulates around the entire chip package, not just between the chip and substrate. But before we get into liquid mold underfill, I want to take a minute to highlight a few different types of underfill.
- Capillary underfill: This is the most common underfill. It’s primarily used with silicon and offers a high level of shock protection and reliability.
- Non-conductive paste: This helps add additional reinforcement when chips are being attached to the substrate. It’s pre-applied to the chip.
- Non-conductive film: This is great for through silicon via die stacking for high bandwidth memory (HBM) applications.
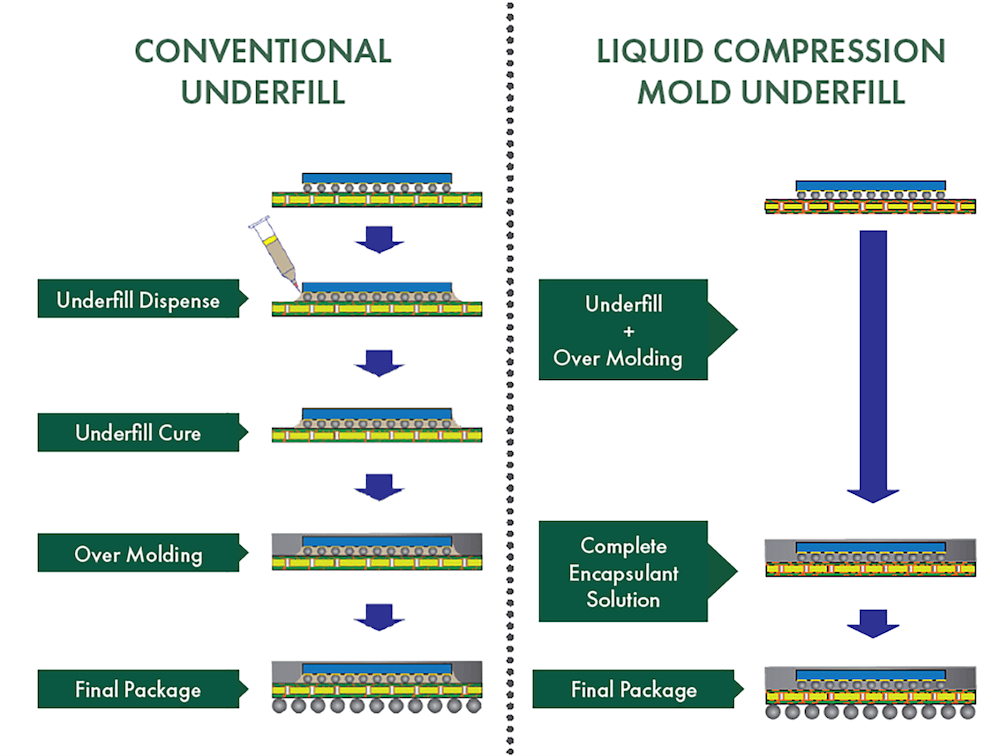
Because liquid mold underfill is used for both over and underfill, Melton says it provides an estimated 70% reduction in process time without sacrificing reliability. To put this another way, it offers a higher throughput than other forms of underfill.
So, why does this matter?
As more technology applications (like advanced gaming processors) require HBM, manufacturing these devices quickly will become essential for keeping up with the rate of demand. In addition, HBM stacks are growing taller to accommodate faster processing speeds. And, as the stacks get taller, the time gained by filling the stack in a one-and-done step will be even more valuable.
After Melton shared the benefits of liquid mold underfill, we focused on the challenges. As he explained, one of the primary hurdles with underfill in general is wafer warpage, which happens when there is a stress imbalance between the front and back of a wafer. To reduce warpage, filling the gaps consistently without defects throughout is key. However, this is not an easy task.
To illustrate, companies like NAMICS are tasked with filling gaps that are 20 microns or less. Twenty microns (short for micrometers), is equivalent to around 0.0008 of an inch. As you can imagine, these gaps are barely visible to the naked eye.
“The key difference with NAMICS material is that it’s liquid mold, as opposed to granular,” Melton shared. “Liquid mold has better gap filling performance, lower warpage, and less particle emissions for cleanrooms.”
At this point, you may be wondering the same thing I was. If liquid mold underfill has all these great benefits, why would someone use any other form of underfill?
Melton explained that although liquid mold underfill is great, it’s still more expensive than other forms of underfill. Because of this, it is best suited for leading-edge technologies, and Melton predicts that it will coexist with other types of underfill for the foreseeable future.
You can learn more about NAMICS liquid mold underfill here.