Fluoropolymers are excellent materials for filters. Polytetrafluoroethylene (PTFE), the same polymer used in Teflon coatings, is inert, stable, hydrophobic, and durable, making it an ideal filtration media. Except for one potential problem.
PTFE is a member of the PFAS (per- and polyfluoroalkyl substances) class. Even though PTFE no longer contains perfluorooctanoic acid (PFOA), the chemical associated with the scandal depicted in Rob Bilott’s book Exposure and the movie Dark Waters, PTFE is still covered by the looming EU ban on all PFAS.
PFAS appears throughout semiconductor manufacturing. One of my Sustainability 101 blogs outlines the extent of these materials’ presence and the challenges in replacing them with PFAS-free substitutes. Finding suitable solutions for some process steps will likely require over a decade of research. That’s not the case everywhere, which is where filtering comes in.
Filters Without PFAS
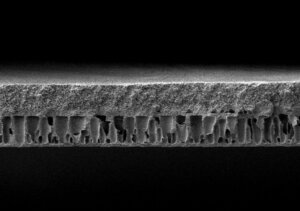
The Fraunhofer Institute for Applied Polymer Research (IAP) continues to lead the way in investigating new materials and processing methods. This month (June 2024), the institute announced that it has developed a non-PFAS filtration membrane for semiconductor applications. The membrane is based on polyacrylonitrile (PAN) that has been chemically modified to enhance its stability in harsh environments.
Fraunhofer IAP’s sample PAN filters have a pore size of 7 nanometers, which makes them suitable for filtering during chemical mechanical polishing (CMP), where filters are essential for minimizing particle contamination. By adjusting the pore size and the number of pores, filters can be tailored to the expected particle size and distribution for specific applications. These filters could be used for everything from incoming process chemicals to wastewater.
This announcement sounds like good news. It is encouraging to see new materials that meet performance requirements while avoiding problematic chemicals and materials. The materials geek in me wants to celebrate this achievement.
I’m all for advances that attempt to eliminate potentially toxic chemicals. Upcoming restrictions from the EU suggest that anywhere we can find an alternative, we should put it in place as quickly as possible. But is focusing on filtration the best path forward?
Do We Need PFAS-Free Filters?
One argument in favor of PFAS-free filters is that this is an application where proof of concept has already occurred. There is no decade-long wait to explore possible candidate materials. So long as the PAN filters last as long as the PTFE ones, it’s a win-win scenario.
It’s worth questioning the order of prioritization in removing PFAS from semiconductor manufacturing, however. The greatest concerns are if these materials enter wastewater streams or if their use exposes workers to toxic fumes.
Filtration is not an especially problematic application for PFAS. Unlike PTFE coatings on cookware, filters are not heated to high temperatures where the material can decompose and release harmful compounds into the air. The polymer is integral to the filter. It doesn’t exist as a coating that can flake off. Its durability and low likelihood of releasing contaminant particles from the filter make it desirable for improving semiconductor yields.
I think we need to look holistically at where in the supply chain PFAS are likely to be released into the environment and prioritize those. We don’t have data on PFAS effluents from semiconductor processing, but we can make educated guesses as to where intentional or unintentional releases are likely. Ironically, regardless of filtration media, wastewater filtration reduces the concentration of chemical byproducts (PFAS-related and others) that accidentally get into local waterways.
We should also consider how much research is required in each application that currently uses PFAS. Where are the opportunities to move more quickly? Qualifying PFAS-free filters for commercial use is probably one of those. Are there other more sensitive applications with a relatively short timeline? It may make sense to start with those unless doing so jeopardizes the R&D investment needed to tackle some of the more toxic, dangerous applications, for which it will take 10 to 20 years of research to find workable alternatives.
I don’t have all the answers. Instead, I see my role as posing questions and helping companies consider new angles. My advice remains the same as when I wrote about PFAS here nearly a year ago. Invest in R&D to move toward less toxic materials and processes while keeping an eye on regulatory restrictions and advocating where needed.