If you are familiar with B Corp certification, you probably associate B Corps with consumer brands like Patagonia or Ben & Jerry’s. Unless, of course, you work at Brewer Science. In 2021, the 3D InCites member became the first company in the semiconductor industry to earn B Corp certification.
Over 6,400 Certified B Corps now operate in 88 countries and 159 industries. The certification process involves many detailed questions about environmental, social, and governance (ESG) issues. Qualifying is not easy. It’s not just a matter of completing a simple application, filling in the boxes, and paying a fee. A company must receive a minimum score of 80 points out of 200 to qualify for initial certification. Companies recertify every three years and only qualify if they show improvement over the previous score.
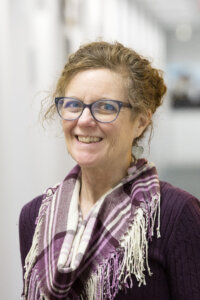
I interviewed Karen Brown from Brewer Science for my upcoming book, Materials & Sustainability. Here is an excerpt from that interview.
Julia: How did you get involved with the B Corp certification at Brewer Science?
Karen: I’ve worked at Brewer for almost 20 years in a variety of different positions in HR, operations, project management, and system admin. In 2018, two executives learned about the B Corp certification. They talked to Terry Brewer, and the three of them and the senior leadership agreed that Brewer Science’s values and vision were a great fit with B Corp certification.
Alan Gerson, our chief legal officer, and Doyle Edwards, director of government relations, approached me. They said, “We know that you are great at managing projects, we know you have a passion for the types of things that B Corps do, we are going to pursue this certification, and we would like you to lead the effort.” We talked with my manager, and she agreed. And then the adventure began.
After we got our certification, we started to do all the follow-ups. The B Lab folks want you to have a point person. And they use all this B-related terminology. The online community, they call the B Hive. And the contact person at each company is called the B Keeper.
So here I am. I got us the certification, and then I’ve been functioning as the B Keeper.
Julia: Who else in your company is involved?
Karen: We have two internal teams going at this point. We had the initial team that we call the B Certified team. That was the group of functional area folks who helped me answer the impact assessment and helped round up all the evidence that we needed to substantiate our answers.
We started with about six people and ended up with ten or twelve. The areas of the assessment match what the B Corp folks call the Five Pillars of Impact. Governance is one of those. I depended very heavily on our finance folks from senior leadership because governance has to do with your written policies, procedures, your transparency, and your ethics. Employees are another one of the areas. So, of course, I relied heavily on several people from HR—recruiting, benefits, finance from a payroll perspective, training and development, performance reviews, etc.
There’s an environmental piece, which for us was the largest piece because, in addition to the five impact areas, every company that gets certified must choose a business impact model. And we chose environmentally innovative manufacturing, so that area became a double whammy. I relied on the EHS folks.
Then we have the community pillar, which is all about people. We added some new folks that head up our community volunteering. There’s a big push on suppliers. So, we have people on the team from purchasing and our supplier management.
And then there’s a pillar called customer, but it’s different from what you would typically think of. It’s not really customer service or customer relations; it’s really about doing business in a way that your customers can have faith in you and trust in you. That you do what you say, and you say what you do. How open are you? Do you allow customers to come in and audit? Do you have certifications like ISO?
After we got certified, our focus shifted more towards informing and engaging our employees with the certification. So, then we have that other team called B the Change. They’ve led some activities, volunteer efforts, and educational efforts to help everybody understand what it means that we’re a certified B Corp. What does that mean for me as an employee if I’m at a trade show or if I’m at a family dinner, and somebody asks me? How do I answer that?
Julia: What advice would you give to other companies in your industry that are considering B Corp certification?
Karen: One of the lessons that we learned and one of the things that I would share with other companies who would decide to pursue this certification is documentation. There were areas where we were doing things and gave ourselves full points when we did the self-assessment but ended up not getting points because we didn’t have a written policy. Or we didn’t have the proper data to back it up.
Another area that we struggle with in our industry is getting local suppliers.
Julia: I was thinking about that because it’s not as though there’s a massive pool of semiconductor industry companies near you.
Karen: We’ve just had to accept it for what it is, and we’ve tried to focus on that non-production supply area. For things like groundskeeping, cleaning services, cleaning supplies, food supplies, and maybe coffee for the break room, each of our local offices will and should give preference to local suppliers. We know we’re not going to get full points. But we’ve done the best we can because we know that, as you said, there are no chemical suppliers in our area.
The same thing goes for diversity and inclusion. Because we are limited in some of the chemicals we purchase for our manufacturing. There are one or two suppliers in the entire world. Where we can, we give preference to diverse suppliers. And we include that in the sourcing. But that can’t be the only criterion.
In the semiconductor industry or in chemical manufacturing, there will be limits to what you can do. It is different than making consumer goods, where you have a lot of choices. If you’re sourcing cocoa beans, for example, you have choices. Some are better than others from the viewpoint of finding local suppliers or supporting diversity.
We’re not ever going to be the perfect B Corp. But as Dr. Brewer always likes to say, and has said since he founded the company, we’re not in business to make a profit, we’re in business to leave the world a better place than it was. For us, that is the way we look at being a B Corp. We’ve now achieved B Corp certification, which validates that we have made and continue to make a positive impact on our community, on our employees, on our customers and, through our suppliers, on the manufacturing process.
B Corp Certification Takeaways
The B Corp journey looks different for a semiconductor company than for a company making consumer goods. Brewer Science has shown that it is possible, especially for smaller companies in our sector that have support at the executive level. If your company wants to improve its social and environmental responsibility and is curious about B Corp Certification, reach out to those who have gone through the process.