If CES® 2022 was any indication, the automotive industry is yet again in the crosshairs of both consumers and industry experts alike. Whether it’s the new electric vehicle (EV) model introductions, color-changing technologies, or concept cars, automotive companies are slowly transforming themselves from manufacturers to technology platform providers. Vehicle electrification is one of those megatrends that has now morphed from a novel trend to an accepted reality. Several environmental, economic, and social factors are influencing vehicle designs and the new powertrain choices. However, some of these choices and corresponding component design and manufacturing aspects may lead to a supply chain evolution in the coming years.
Market trends in vehicle electrification
CO2 emission mandates set by various regulatory agencies are driving electromobility growth. For example, as shown in Figure 1, the chart on the left shows normalized CO2 emissions for each of the four major automotive markets, while the chart on the right shows how CO2 emissions can be reduced by various degrees of electrification. The internal combustion engine (ICE) has nearly 100% carbon emissions. In contrast, mild hybrid electric vehicles (MHEV) use a small motor to aid the ICE, providing a 15% emissions reduction. A battery electric vehicle (BEV or EV) uses only a DC battery and motor and thus produces no carbon emissions. Through various powertrain architectures and proliferation, within the next five years, nearly 25% of all vehicles produced will be electrified with the number increasing to around 50% by the end of 2030 [1]. This huge growth is due to increases in expected demand, reductions in the cost of the DC battery, and anticipated growth in the charging infrastructure.
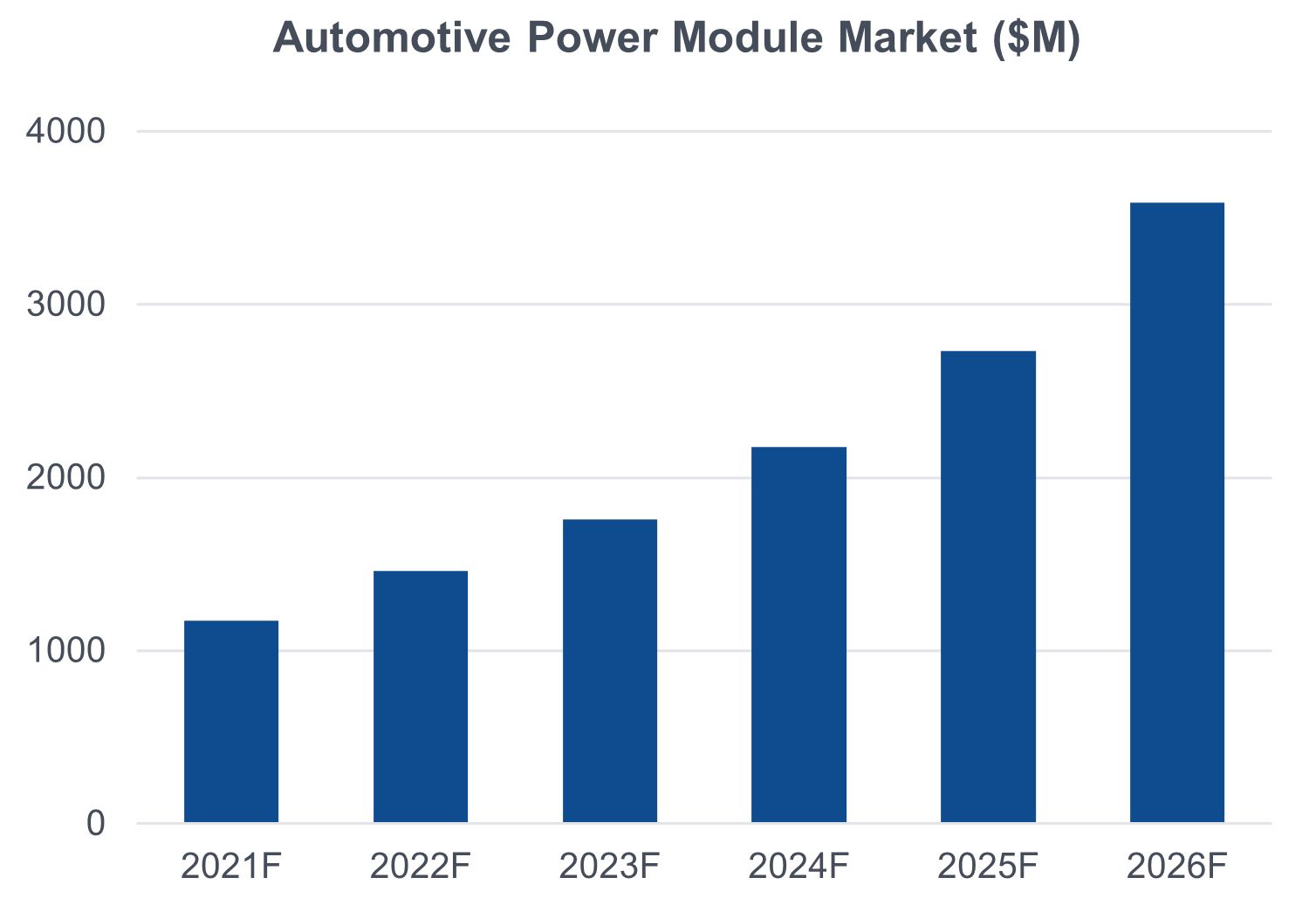
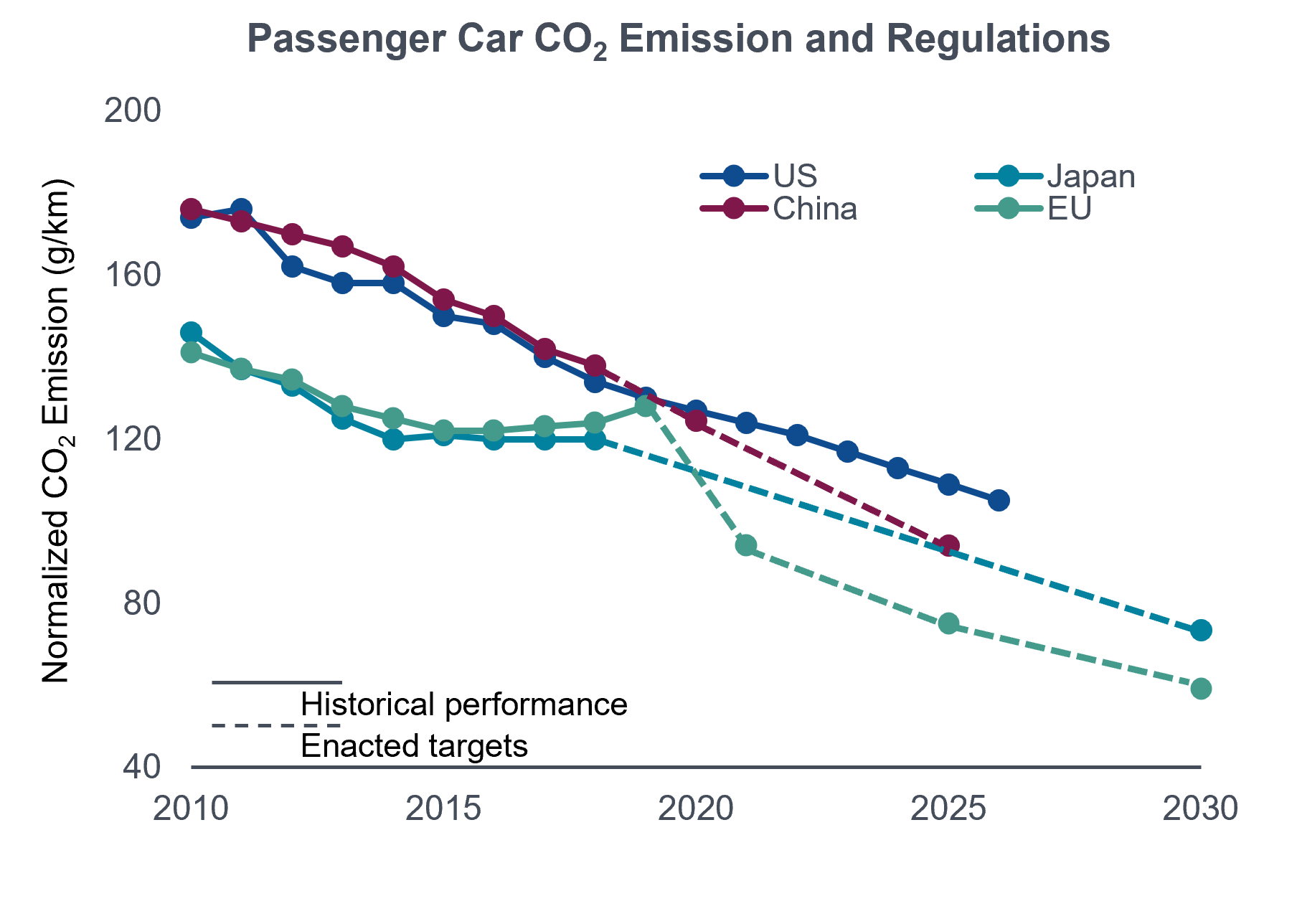
As a result, power semiconductors used in powertrain systems for vehicle electrification will see huge growth. To better understand this growth, let’s examine a simplified schematic of an EV powertrain (Figure 2). The critical blocks that enable the main functionalities are the onboard charger (OBC), DC/DC converters, and the main inverter. The critical components that enable each of these circuits are power devices, used as switching elements. At the system level, a key priority for EV designers is maximizing the efficiency of all these circuits to enable a better range between each battery charge. As the system requirements increase, so do the requirements on the cost ($/kW) and power density (kW/l) of the power electronics. Currently, cost targets are roughly 5 $/kW, whereas power density is around 12 kW/l. These targets are expected to reach 3 $/kW and 60 kW/l by 2035 [2]. To achieve these goals, semiconductor suppliers need to offer superior solutions including newer power technologies such as silicon carbide (SiC) and gallium nitride (GaN) devices, and use cost-efficient power module packages.
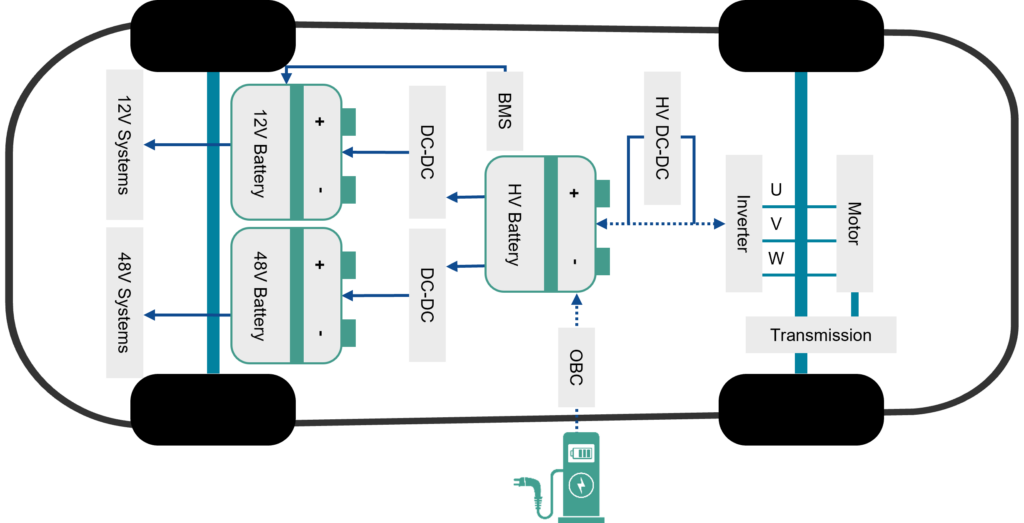
Power Module Packaging
In main inverter applications, power modules must address performance and reliability targets within thermal, electrical, and mechanical constraints. While the bulk of the electrical performance is addressed by the semiconductor devices, power module packaging plays a vital role in meeting the thermal and mechanical targets. However, electrical performance can also be improved by reducing parasitic resistances (R) and stray inductances (Ls) of the package. Ls is especially important to reduce overshoot voltages during switching; Ls of a power module results from the substrate metal parts, wire bonds, and lead frame/bus bars. One of the ways to minimize these losses is to reduce the current loop geometrical length and area. Wire-bond-free concepts such as double-sided soldering and sintering on ceramic substrates are better solutions to lower Ls. One such solution, a double-sided cooling (DSC) molded module, is shown in Figure 3a, where wire bonds are replaced with sintering for the current path between collector and emitter of the insulated gate bipolar transistor (IGBT) switch. The DSC module structure not only reduces the electrical parasitics but also offers enhanced thermal efficiency by removing heat from the top and bottom sides of the package through the substrates.
Power cycling and higher ambient temperatures subject power modules to large temperature excursions. So, a cooling system that does not complicate system design and increase cost becomes increasingly important. One way to address these concerns is power module designs with pin-fins (Figure 3b) that share the cooling system used by the motor or engine. For extended reliability, heat must be dissipated effectively, which can only be achieved using low thermal resistance materials. Higher thermal conductivity ceramics such as aluminum nitride (AlN), silicon nitride (Si3N4), and copper (Cu) with a direct cooling structure can be used to reduce the overall thermal resistance. Whether it is a baseplate-free solution such as a DSC module or a pin-fin power module, the packaging industry needs to consider several technologies for next-generation power modules. These include interconnection advancements such as thick gauge (>5 mil) Cu wire, Cu clips, advanced substrates such as Si3N4 with active metal brazing (AMB), die-attach and substrate attach using silver (Ag) or Cu sintering, Cu or AlSiC baseplates, and silicone gel or epoxy resin encapsulation.
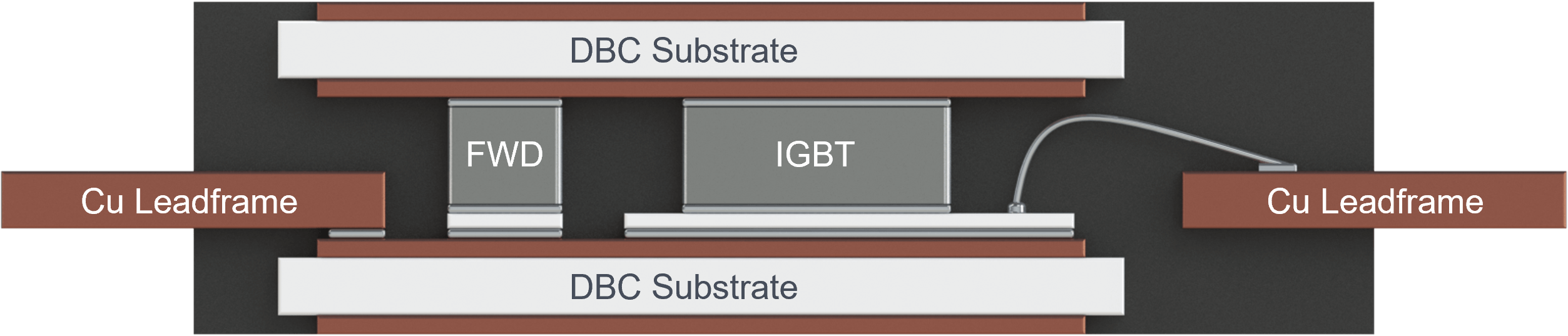
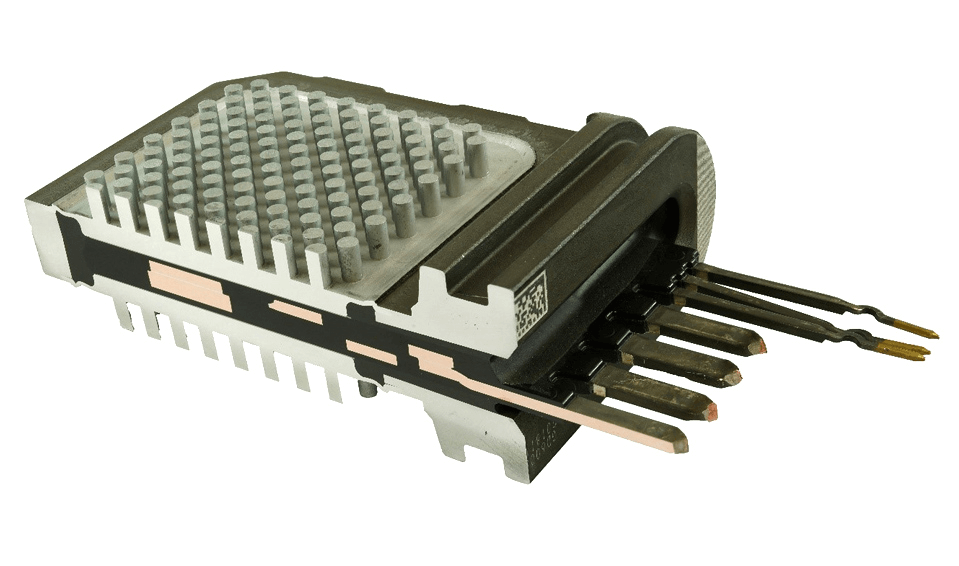
Supply Chain Evolution
The power module packaging market has long been fragmented and dynamic. To understand the appeal of this segment, let’s look at the module cost breakdown as shown in Figure 4a. Manufacturing and raw materials are nearly 55% of the total module cost [3]; in a power discrete package, these same elements are generally < 20% of the total cost. Historically, power module manufacturers have supplied relatively low-volume and high-price market segments such as industrial, rail, and renewable energy. Given the impending growth of the power module market due to vehicle electrification (Figure 4b) [3], the module supply chain may see several changes. For example, non-automotive suppliers with power module expertise can either choose to expand into the automotive market by themselves or by partnering and licensing technology with traditional automotive suppliers. In situations where traditionally closed geographical ecosystems existed, some suppliers have started to diversify their business or regional portfolio. The geographical expansion has increased to take advantage of packaging technologies such as substrates, die-attach, and encapsulation.
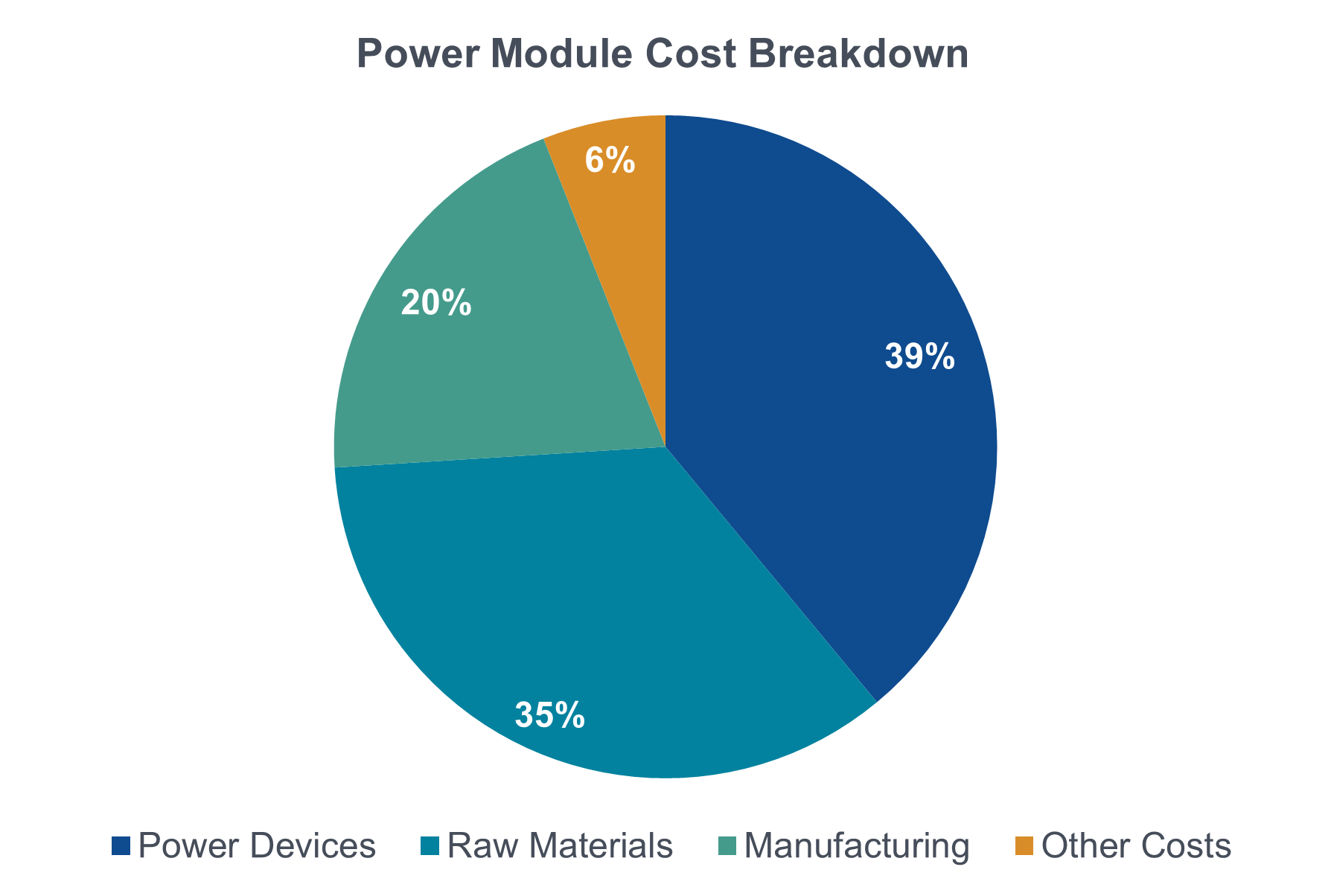
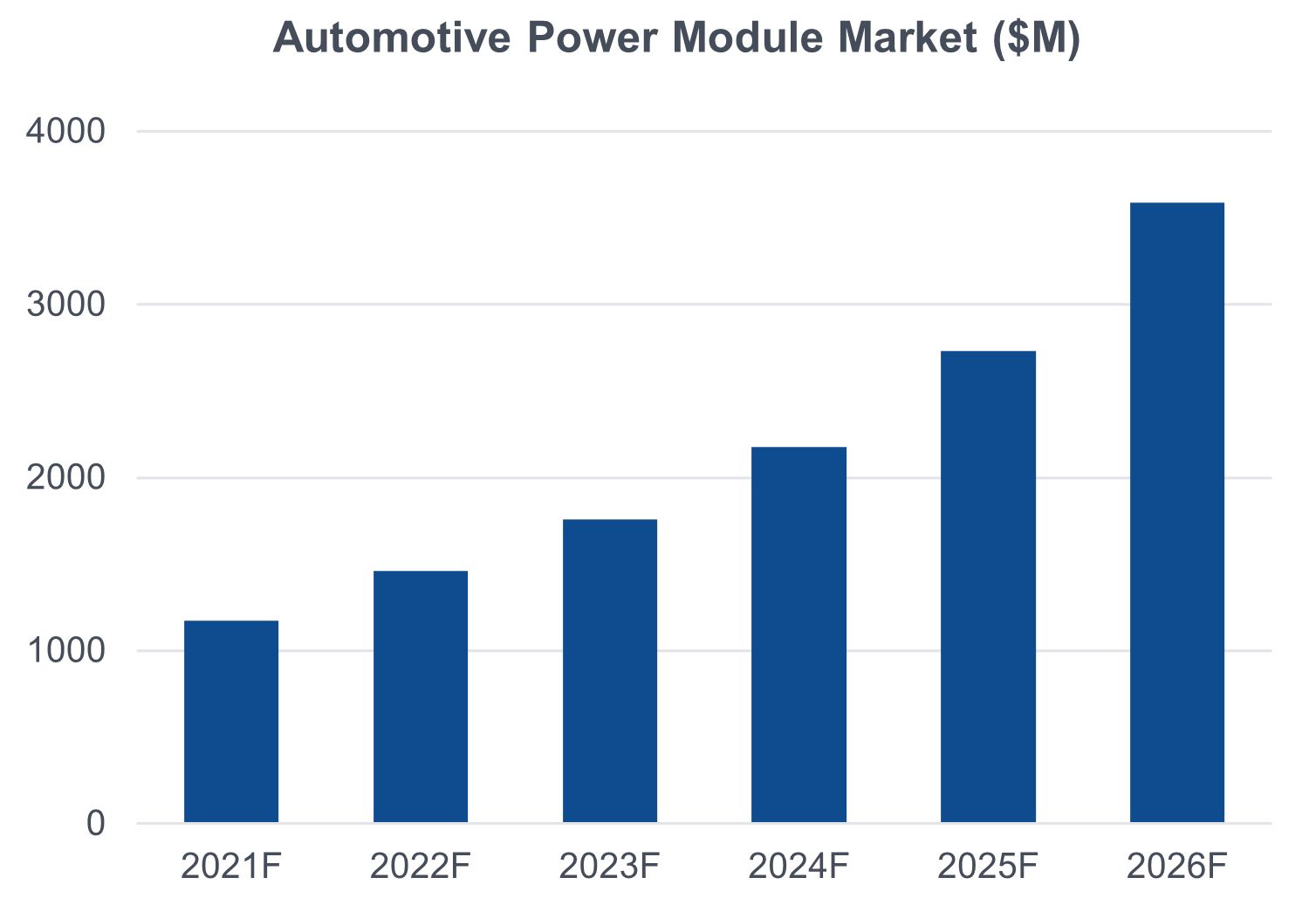
The automotive industry has long been a high-volume, low-price arena. With the growth in the power module market, competition will increase and suffer from price pressures leading to partnerships to reduce costs and simplify market entry. On the positive side, module technology is well understood, and suppliers have known to release products with excellent performance and reliability. For non-power module makers such as outsourced semiconductor assembly and test (OSAT) suppliers, entering the power module market presents an appealing case since they can easily leverage their current expertise in ramping products to high volume with proven reliability and an appealing cost structure. One final factor that is favorable for OSATs is automakers increasing willingness to venture deep into the supply chain for the inverter module design to differentiate themselves from competitors and to control costs.
Conclusion
Backed by the strong electromobility trend, the automotive power module market is expected to see a compound annual growth rate (CAGR) of 25% from 2021 to 2026 [3]. With high performance and high-reliability semiconductor technologies readily available, the design and cost of power modules could become a differentiation factor for automakers and their Tier1 suppliers. At the same time, there is a strong desire from vehicle manufacturers and Tier 1s to create a transparent and shortened supply chain. As a result, both of these groups should focus on co-development efforts and partnerships directly with OSATs to accelerate go-to-market timelines and provide sustained profitability.
References:
[1]. Credit Suisse, “Automotive Semis: Powering the EV Megatrend,” Mar 22, 2021.
[2]. Automotive Council UK, “The Roadmap Report | Towards 2040: A Guide to Automotive Propulsion Technologies,” 2018.
[3]. Yole Développement, “Status of the Power Module Packaging Industry Report YINTR21196,” Nov. 2021.
[4]. Infineon Technologies AG, “Company Presentation”, Nov 2021.
[5]. SystemPlus Consulting, “Power Electronics Electronic Catalogue,” Nov 2021.
© 2022, Amkor Technology, Inc. All rights reserved.
This post originally appeared in the 2022 3D InCites Yearbook. Read the full issue here.