Understanding the role of compromises and trade-offs in the design process
Electronic packages serve many purposes including protecting, connecting, and cooling a device. If any of these are done improperly, the chip is rendered inefficient at best or useless altogether. For that reason, the design, construction, properties, and capabilities of the package selected are critical to ensure optimal device performance.
Temperature is one of the main factors that affect performance. High-frequency devices can suffer a loss of efficiency as temperatures at the chip level increase. Every degree of heat that can be dissipated adds to the efficiency of the device as well as to its useful life.
The package plays a significant role in thermal management. Proper thermal management is essential for high frequency and high-power semiconductor devices such as gallium arsenide (GaAs) and gallium nitride (GaN). In particular, GaN-on-SiC devices have incredibly high power densities and the design of the electronic package can dramatically affect their performance.
Several types of engineers are typically involved in the electronic package design cycle. Mechanical engineers, materials engineers, electrical engineers, and thermal engineers contribute most often, but sometimes manufacturing or industrial engineers might also be included. So, the compromises and trade-offs begin at the engineering level but don’t end there. People from the accounting, quality, purchasing, assembly, and sales and marketing departments may also have input.
Within this assortment of people that have such different levels of education, experience, and expectations, it can be difficult to please everyone. The person in charge of the final package design, more often than not, feels pulled in a lot of different directions. But if everyone understands that many issues beyond their own must be considered, the team can achieve a workable design that meets the customer’s major objectives.
Package Layers
Thermal considerations address two areas, thermal expansion, and thermal conductivity. A useful tool in considering electronic package designs is to consider the package as a series of stacked layers. Working with and thinking about packages in terms of layers can simplify thermal dissipation and expansion analysis. Viewing packages as layers is a useful way to understand 3D interactions in the package structure. This is the basis for thermal simulation modeling.
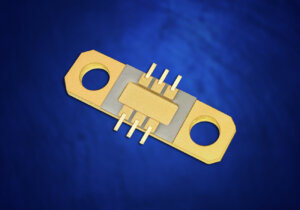
The leaded power amplifier (LPA) package is an example of layered construction. It begins with a combination base and heat sink, topped by an alumina insulating layer, a metal lead frame, and a lid. (Figure 1.)
The surface mount power (SMK) package is very similar to the LPA package but has vias to carry the signal from the top conductor pads to the bottom of the package. The leads on the bottom of the ceramic are coplanar with the bottom of the base. With the leads trimmed short, this package is appropriate for surface mounting (Figure 2.)
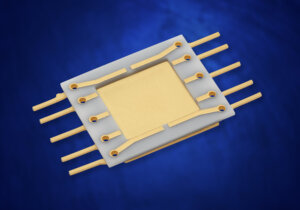
The LPA and SMK package examples are ideally suited to many power amplifier applications. They use a single heat sink layer of copper composite or copper laminate that has high thermal conductivity and is also well matched to the temperature coefficient of expansion of most devices. It’s also convenient that they are designed to operate over a broad range of frequencies. LPA packages have excellent performance from DC to 23 GHz and have bolt holes for securing the package to the printed circuit board (PCB) and chassis. SMK packages operate from DC to 26 GHz and have the convenience of being surface mounted, which simplifies the PCB design.
Conclusion
Many factors need to be considered when designing the optimum power amplifier package, including thermal dissipation and expansion requirements. Usually, no single consideration can dominate, so the design decisions end up as compromises. One simple method to aid understanding of the issues in assembly and function of the package is to view the package as layers. This simple analysis is useful to understand both the CTE and heat flow. Simulation tools can be used to analyze the impacts of expansion mismatch and thermal conductivity on the reliability and performance of the final assemblies. These tools can be used to estimate if material choices are practical and to what degree a material or design change will impact a performance parameter of the package.