Artificial intelligence and machine learning (AI/ML) can have various applications in smart manufacturing for semiconductor fab, advanced packaging, and electronics manufacturing, and it typically involves several key elements: sensing, connectivity, predicting, and control. As recognized by many industry organizations, smart manufacturing matures through several levels: reactive, preventive, predictive, and autonomous (Figure. 1).
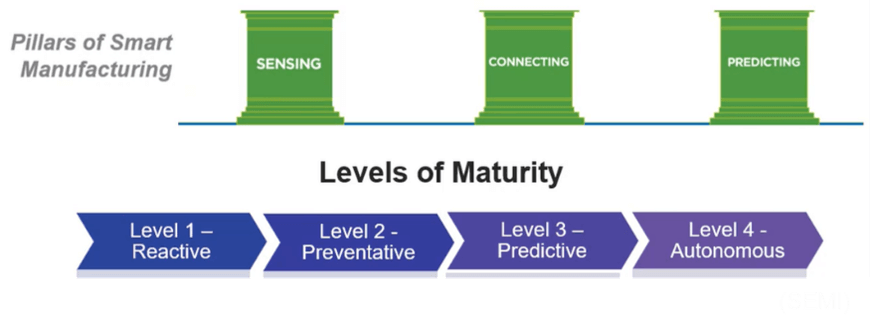
Figure. 1: Pillars and maturity levels of Smart Manufacturing (Source: SEMI).
Adaptive control is the “holy grail” in AI/ML for semiconductor smart manufacturing. There are various AI/ML platforms in the industry that can be used for supply chain management, new product introduction (NPI), production planning, traceability, all the way to predictive maintenance, productivity improvement, process, and yield improvement, etc. The latest AI/ML platform can take you right to the highest level, with sensing, connectivity, predicting, and control all-in-one while providing a scalable, open, and cost-effective platform that seamlessly and progressively integrates all the key elements (Figure. 2).
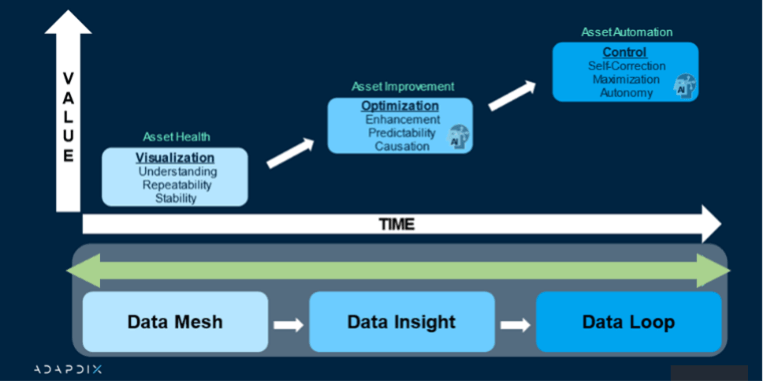
The AI/ML platform can utilize data from existing sensors within the machine, often without the need for additional sensors. The edge-first solution can integrate into other cloud and edge-based services, allowing legacy system data connectivity to nearly all major automation vendor components and providing flexible data management tools to move OT data securely and reliably across complex enterprise edge to cloud network architectures. The ML models offer the capabilities for predictive optimization – for machine performance and for the manufacturing process, and its control intelligence capability can work directly with the machine, once approved by the customer, for adaptive control of the machine itself. As such, the AI/ML platform not only offers capabilities for observability and monitoring, but also further offers great capabilities for predictive analytics, optimization, and control (Figure 3).
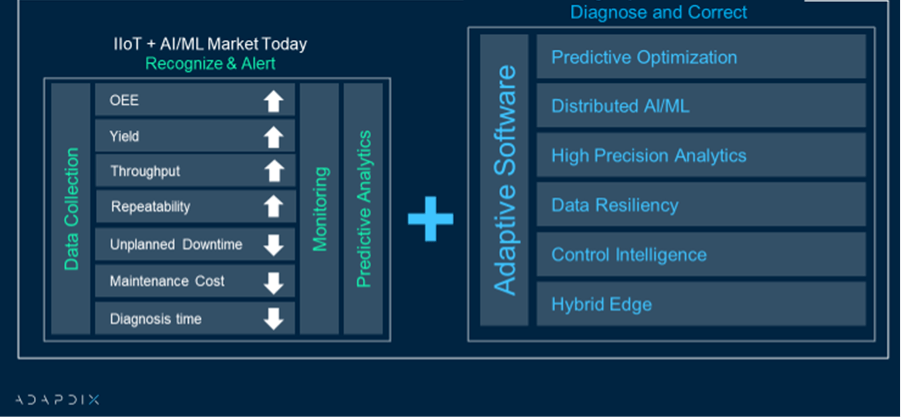
Edge Based Architecture
As an example, the software solution combines advanced AI/ML with a distributed, edge-based architecture (Figure 4). The platform connects and ingests multiple edge data streams (e.g., process logs, machine data, and instrumentation data in a time-synchronized fashion) in real-time – within millisecond cycle time. It can also collect full-stack data from the customer’s end-to-end operations and perform real-time synchronization and validation of critical system data.
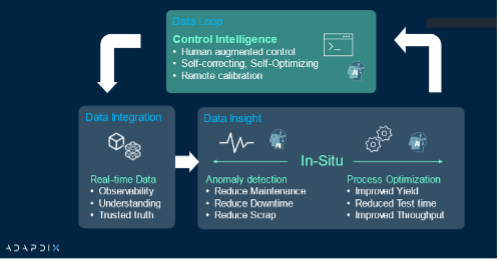
The flexible and containerized architecture can support a variety of protocols at the edge (including proprietary brownfield protocol deployments), thus allowing the platform to easily integrate with industrial equipment for data ingestion. The open and scalable architecture built specifically for the distributed edge environment can help avoid the overhead of moving all data to the cloud or centralization location from the get-go. The open and extensible architecture allows the platform to support edge to hybrid-cloud deployment topology for easy integration with 3rd party technologies.
As such, global enterprises can easily integrate their Digital Transformation technology ingredients such as data virtualization and unsupervised learning on the edge, and transfer learning between machines, manufacturing lines, and geographically distributed sites in a scalable, flexible, and cost-effective manner. This allows the customer to be cloud-agnostic and accelerate innovation to achieve tangible transformational business outcomes.
The inferencing models capture, store, and analyze real-time data at the edge, delivering predictive data intelligence for production environments in milliseconds. The time-triggered architecture can predict, at the millisecond level, whether data readings monitored are within a permissible range, for example. If data goes out of range, several different reactions can be triggered. It puts the customer back in control of their production systems without the need for costly systems integration and time-consuming IT implementations. Once the ML models have become mature, with the customer’s approval, the platform can work directly with the machine itself for adaptive control and optimization.
Smart Manufacturing Applications
The AI/ML platform can be quickly deployed – in most cases providing same-day access to critical system-level data that, working with the ML models to be developed over the period of several weeks, enables the customer to predict equipment degradation, prevent faults, reduce unplanned downtime, and improve asset health and utilization. The platform enables customers in the semiconductor industry to transition from relying on reactive maintenance strategies to predictive monitoring and control of their end-to-end operations, often with increasingly complex machinery and systems. The no-code/low-code solution can be deployed quickly and easily, and scale as the needs grow. Further, the platform not only performs predictive analytics on manufacturing equipment but also is able to test and control it remotely, if needed.
Observability, visualization, and traceability can all be realized from the site or line-level all the way down to machine sensor level, with granularities unimaginable before, offering unprecedented insights and intelligence for optimization and continuous improvements. The ML models, through continuous refinement in real-time, are used for predictive maintenance (by anomaly detection) and more importantly, for adaptive control of the machine and process directly.
These capabilities have been leveraged by several large global enterprises for semiconductor fab, advanced packaging, fiber optics for transceivers, precision placement for SMT, and other challenging processes, with significant improvements in process yield, while reducing cycle time and machine downtime. This is particularly helpful when there is capacity shortage in the semiconductor industry. For example, a large, multinational semiconductor company deployed the AI/ML platform to manage its microdevice assembly production line. All equipment motor axis movements, component gesture movements, and subsystem positions are tracked every 25 milliseconds to minimize any unplanned downtime. The software platform runs locally at the customer’s facility to maintain data security from external risks and to ensure ultra-low latency program execution times.
As the platform is machine agnostic, it can be deployed onto various machines on the line across the factory. This is particularly powerful as upstream and downstream machines can now “collaborate” for overall synchronous optimization. Complex models that involve multivariate relationships between data sources, operating in-situ – at “process speed” – can be delivered.
There are many potential AI/ML applications for intelligent edge automation in smart manufacturing for semiconductor fab, advanced packaging, assembly, and test. It is a critical tool to enable innovations in the industry as advanced technologies demand increasingly more complex manufacturing processes. For further information, please contact dshangguan@adapdix.com.