This past fall, our packaging industry saw significant shortages of packaging substrates made from Ajinomoto Build-up Film (ABF). Let’s take a closer look.
Ajinomoto is not your typical electronics materials company. Its main product lines are food seasonings, amino acids, and pharma products. The company entered the electronic materials industry in 1996. Its first ABF customer came online in 1998 (Figure 1).
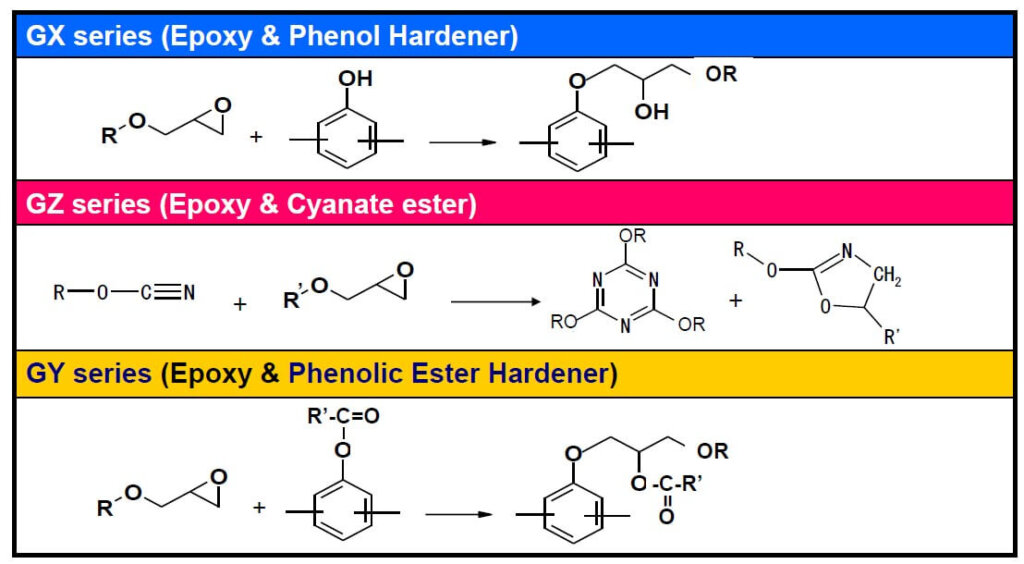
Chips that use laminated packaging often use IC substrates which are made with ABF. The process flow for using ABF to fabricate build-up substrates is shown in Figure 2.
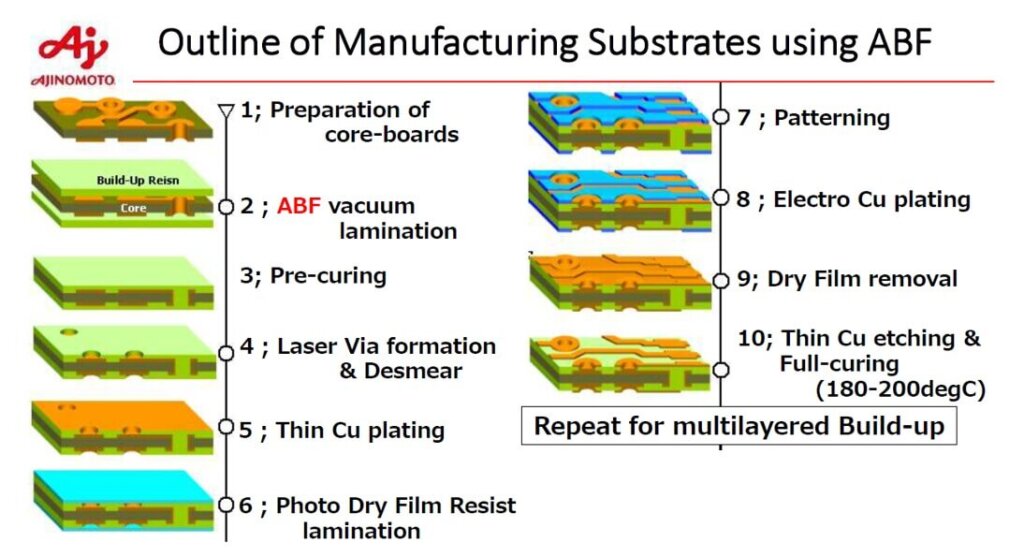
A cross-section of a typical substrate is shown on th right. For those interested in a nice tutorial on “Build-Up Films for Flip Chip Semiconductor Substrates” check out the Jeff Gotro blog.
For the past several years, IC substrate suppliers have been cautious about capacity expansion due to the flat PC market. More recently, requirements of big data handling have stimulated demand for ABF substrates needed to package complex ICs.
Also, suppliers of ABF substrates reportedly experience yield issues with their advanced products which result in a decrease in potential production quantities. The yield of ABF substrate production at Taiwan-based suppliers Unimicron, Nan Ya, and Kinsus are reportedly 70% or lower for high-end offerings, according to Digitimes.
All three of these substrate suppliers are trying to expand production, but reportedly will only be able to boost it slightly during 2021 – 2022.
Unimicron will reportedly be the major ABF substrate supplier for Apple’s new Mac computers powered by Apple’s in-house developed ARM processors. Unimicron, which suffered fires in its substrate plants in Oct 2020 and Feb 2021. has seen its supply of ABF substrates fall short of demand. The company’s tight supply has prompted its customers such as AMD to shift orders to other substrate suppliers including Nan Ya and Kinsus. Kinsus has a global market share of about 6% for ABF substrates and 30-40% of its ABF substrates are used in packaging ICs for PCs, servers, and networking/communication equipment. Kinsus reportedly will build new ABF substrate production lines in northern Taiwan, with the new capacity slated to come online in the fourth quarter of 2021.
In Aug 2020 Kinsus’ increased its monthly production capacity to 12 million ABF substrates. The company plans to further expand the monthly production capacity to 16 million substrates in 2021. While Xilinx used to be the largest client for ABF substrates for FPGA packaging, Kinsus has obtained orders for ABF substrates from additional clients including Broadcom and Nvidia.
ABF Build-up Substrate Shortages Causing Infrastructure Problems
Over the past 6 months, there have been repeated build-up substrate shortages reported. When TSMC can’t buy enough ABF substrates, the impact affects the whole market, i.e Apple, Qualcomm, and Samsung who all use ABF substrates as well. DigiTimes reported on a shortage in both the summer of 2019 and the summer of 2020 and claimed it could widen and worsen in 2021.
Finally, in Dec of 2020, we had the headline story on how “The worsening shortages of ABF substrates are expected to become one of the major woes affecting shipments of new CPU and GPU products at chipmakers in 2021”.This does not appear to be a story that’s going away.
IFTLE NOTE – just another reason to “re-shore” state-of-the-art packaging in the USA.
There are rumors that AMD can’t currently meet the demand for notebook computers because of the ABF problem and that the issue could worsen in Q3 2021 when Zen 3 notebooks come to market.
TSMC is reportedly overwhelmed by demand. Many of the 2020 product launches relied on 7nm chips from TSMC. ARM manufacturers such as Qualcomm also use 7 nm and have moved capacity from Samsung to TSMC. TSMC is currently pretty much alone in the market with this technology and the production lines are therefore working at full capacity. A sudden increase in production is therefore not possible. The ABF substrates are needed for many of these products.
Global Wafer Capacity Consolidation Continues
IC Insights has released a new “Global Wafer Capacity 2021-2025” report which provides a ranking of the 25 largest wafer capacity leaders as of Dec 2020.
The combined capacity of the top five suppliers represented 54% of the total global wafer capacity in December 2020 compared to 2009 when the top five leaders accounted for 36% of total capacity. We should note that four of the five are memory suppliers (Table 1).
Samsung represents 14.7% of the world’s total capacity. TSMC with about 2.7 MM wafers/month capacity, represents 13.1% of world capacity. Micron has 9.3% of worldwide capacity, SK Hynix 9.0%, and Kioxia (Toshiba) 7.7%. The next 5 include Intel (884K), UMC (772K), GlobalFoundries, Texas Instruments, and SMIC.
In terms of foundries TSMC, UMC, GF, SMIC, and Powerchip are each ranked within the top 12 world capacity leaders having a combined capacity of 5.1 MM wafers/month representing 24% of the total world fab capacity.
For all the latest on Advanced Packaging stay linked to IFTLE……………………………..