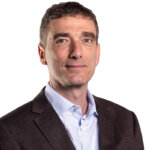
50 years of providing specialized thermal solutions to the semiconductor industry is a significant accomplishment. It means your company is nearly as old as the industry itself and has successfully evolved right alongside it. So ERS electronic GmbH, located in Germering, Germany, was ready to celebrate in a big, big way – Munich style. There was going to be a giant summer party, and all the customers, partners, and current and former employees were invited. There was going to be a big tent, a band, lots of food and of course, beer. Sophia Oldeide, ERS PR, and marketing communications manager had it all planned.
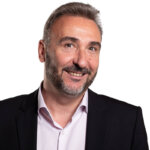
“Even though we have become such an international company in the past few years, we felt it was important to emphasize that we are a German company that started in Europe,” she said. “We wanted to make the celebration about the employees as well, because many of them have been with us for decades, and it should also be about them.”
And then along came COVID 19, months of quarantine, stay-at-home orders, and social distancing. Plans for the party were tabled, at least for now. Instead, the company is taking to social media, sharing stories, videos, and milestones about ERS’s first 50 years. As ERS is an active member of the 3D InCites community, we wanted to help them share their story. So, I hopped on a Zoom call with Co-CEOs, Klemens Reitinger, and Laurent Giai-Miniet, so I could share its origin story, its impact on the industry through the years, highlights, and future plans.
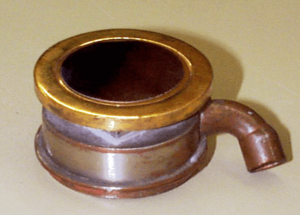
Thermal Solutions for Wafer Probe
As with many technology companies, it began with a single invention. Klemens’ uncle, Erich Reitinger worked at Schlumberger, a company that originated electronics sensing and measurement instrumentation for mining, oil exploration, and other industries. IBM was building a semiconductor line in Stuttgart and purchased a probe tester from Schlumberger. “The engineers noticed that the test results changed when the device came under temperature,” explains Klemens, “So my uncle came up with a good idea: a 1 ¾ inch chuck with an integrated liquid-cooled Peltier device.” (Figure 1)
IBM did what IBM usually does: they self-built a wafer test prober. But the thermal part was tricky. They wanted to outsource the chuck to Erich Reitinger. So, he left Schlumberger to start Erich Reitinger, Special Developments (Sonderentwicklungen) – which morphed into ERS Electronic. “ ’Special Developments’ was because he was always thinking on the edge of technology and planned to develop other solutions. He never expected the thermal chuck to become THE product for ERS,” said Klemens.
Influencing the Industry
ERS was not just along for the semiconductor industry ride. Its innovations continually paved the way for advanced solutions for 50 years. For example, not only did Erich Reitinger develop the first thermal chuck based on Peltier cooling, ERS developed the first thermal chuck for ice-free testing down to -55°C that could be integrated into an automated wafer prober
When liquid cooling no longer met the industry’s requirements for efficiency and stability, they invented the first 100% air-cooled thermal chuck (Figure 2). This technology was enhanced further to use recycled air and deliver cold test solutions for wafer-level test in an ice-free environment. Most recently, the company invented thermal chuck solutions for ultra-low noise temperature testing, as well as high thermal uniformity designed for testing high-precision, humidity, and pressure sensors.
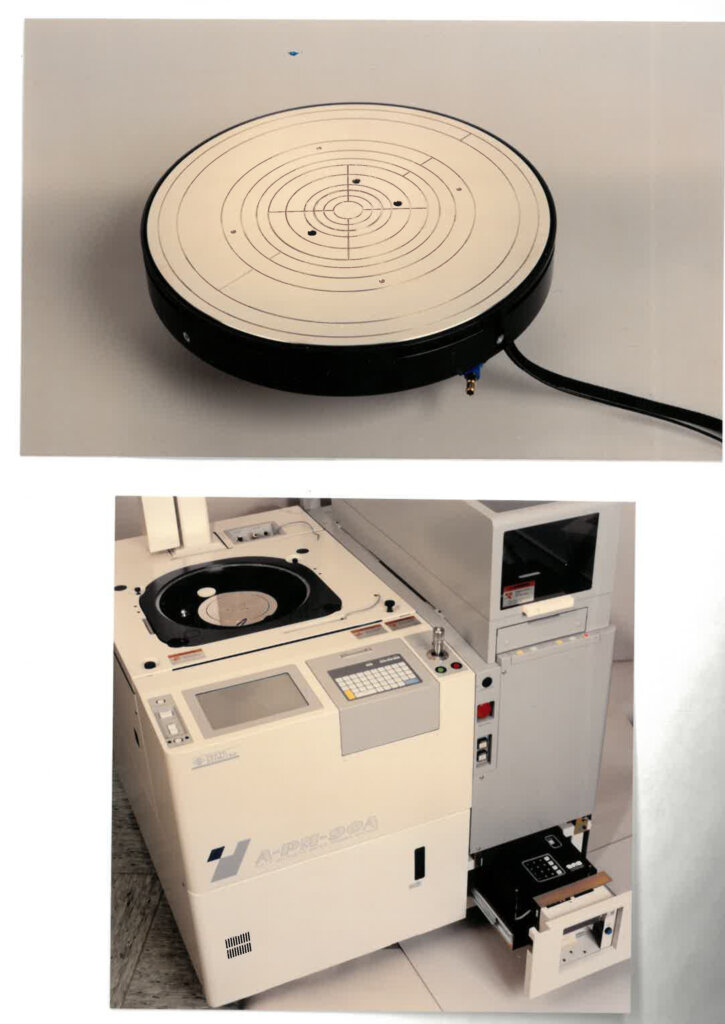
Foray into Thermal Solutions for Fan-out

Test is not all that ERS does. One pivotal moment for the company was the arrival of an embedded wafer level ball grid array (eWLB) technology. ERS put its thermal expertise to work addressing a need for thermal debonding solutions that also controlled the wafer warpage. In this space, ERS technology sits at the junction of thermodynamic, electronic, and micromechanical technology. “When customers need a chuck that provides more active control of temperature, they come to us,” says Klemens. “We can even control the temperature between 450°C and 500°C, which is not easy.”
Taking a Small German Company Global
Klemens did not plan to follow in his uncle’s footsteps. Born in Vienna, Austria, he came to work at ERS in Munich to make money while he was in school, where he was studying to be a technical engineer. As there were no high-tech opportunities in Vienna, he moved to “the small village” of Munich. He viewed ERS as a small company on the cutting edge, but not many people who worked there knew how semiconductors are made. He saw the chance to grow with the company. “I’ve worked in every aspect there, and when it was time for my uncle to retire in 2008, selling it to me was a logical move,” he explained.
Four years ago, he brought Laurent in as co-CEO and head of sales and marketing. Since then, the company has grown from a small, German operation serving primarily European customers, to a global operation with a solid footprint in Asia Pacific.
ERS Today
As wafer probing became a critical step in semiconductor manufacturing, independent companies started manufacturing probe test systems: Accretech, Tokyo Electron (TEL), FormFactor, MPI, and others. Many of them turned to ERS for is solutions for testing under temperature, and other special environments, such as anti-magnetic test.
According to Klemens, 90% of ERS chucks go into probe stations. And with the rise of 3D integration and advanced packaging, it’s become a very interesting field with a mix of classic and back-end testing applications. “Anybody doing test is a potential customer for us,” he said.
According to Laurent, ERS’s Thermal Chuck customers are a 50-50 split between machine makers and semiconductor manufacturers/OSATs. Certain device types, such as high-precision analog, RF devices, high voltage, and high-precision sensors for automotive applications call for testing at temperature, and not all probe testers can accommodate these needs. Additionally, it’s more economical for OSATS who sign new customers in these spaces to upgrade their probers to offer tri-temp solutions.
“We have sold our solutions to every single prober manufacturer,” said Laurent. “Some developed their solution internally but come to us for specialty chucks. We also sell to semiconductor manufacturers who are not happy with the ‘off-the-shelf’ solutions. They buy the tools and then integrate the ERS chucks into them.”
“That’s why ordering tools without the chuck is accepted in the industry,” explained Laurent. “Customers say, ‘don’t bother. We’ll put an ERS chuck inside.’”
What’s Next for ERS?
As Fan-Out moves into panel format, ERS plans on being ready with its first fully automatic debond and warpage correct system for panel-level packaging. Additionally, “The world of sensors calls for more challenging tests with precision measurement. This is a new space for us,” says Reitinger. Pressure sensors, 5G, and power management ICs are driving new developments in automotive application requirements. Reitinger says they are exploring new substrates such as silicon carbide and gallium nitride, which are critical in this space.
And of course, the celebration that was supposed to take place in 2020? It’s still going to happen. It just may be held in honor of ERS’ 51st Anniversary. ~ FvT