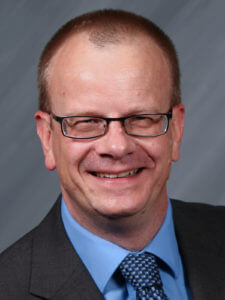
“We believe that materials science changes the world,” declared Indium Corporation’s Andy Mackie during our recent sit-down together at IMAPS 2019 in Boston, MA. Even though I am a chemical engineer myself, and not a materials scientist, Andy Mackie, Ph.D., senior product manager, is reaching the choir, one engineer to another, right from the start, talking about Indium Corporation’s materials-centric perspective on changes and challenges in the advanced packaging world.
2019 has been a banner year for Indium Corporation in general, and for its solder products, for its flux products, and also, more specifically, for its sintering products. Founded in 1934, and going stronger than ever, Indium Corporation is, as evidenced by its significant participation at IMAPS 2019, both in the number of talks and posters presented during the Symposium (six, by my count), and by its prominent, and busy, exhibit floor booth, one of the giants on the materials-side of semiconductor device packaging.
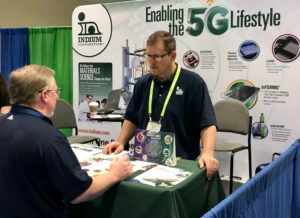
Besides the “tons of stuff coming down the line” from Indium, Andy said, there are a satisfyingly large number of current successes of note, most of them the result of development programs in which the company’s scientists and engineers worked directly with equipment manufacturers and, ultimately, with end customers, and customers of the end customers – think of Indium Corporation working with jetting solder paste equipment suppliers to address the needs of the smartphone world, for example, and you’ll get the idea.
Or this: in the automotive space, the integration of RF components and logic components needs to be completely reliable, at an automotive quality-level of reliability, which means that residues potentially created during the die-mount and flip-chip packaging process aren’t tolerated at all, as these residues can introduce subtle sources of mechanical damage; damage that negatively

impacts system reliability in a product, your car, expected to last fifteen years or more during operation in all sorts of challenging environments – Pennsylvania in the winter, Phoenix in the summer, the Mission in the rain.
Indium Corporation has an answer for that: Flip-Chip Flux NC-26s.
The Materials Science of Large Format Substrates
A third example of recent work from Indium Corporation is in a packaging technology close to my own heart, which is the area of large-format substrates – fan-out panel-level packaging (FOPLP), specifically. As Andy explained, one of the key challenges of using large substrates in FOPLP is the relative quality of the large (600mm x 600mm) substrates themselves when compared to the more familiar and more forgiving 300mm round substrates used in fan-out wafer-level packaging (FOWLP). Panel warpage, compared to reconstituted wafer warpage, can be extreme.
Andy went on to say “Typically, the last stage of the FOWLP manufacturing flow is the ball-attach or bumping process before package singulation. For the ball-attach process, flux is usually printed on the reconstituted carrier, and spheres are dropped onto the flux, then reflowed and cleaned. The FOPLP redistribution layer (RDL) is vastly different from that of standard flip-chip substrates, necessitating a flux with appropriate properties to meet yield targets and eliminate emergent failure modes.”
But the optimization space here is a large one, filled with controlled, uncontrolled, and, probably, confounded variables, so the performance targets might be moving, at least as far as panel sizes go. “New materials are being investigated for different types of FOWLP, with different redistribution layer materials, low-k dielectrics, passivation layers, solder resists, etc. The compatibility of fluxes with these materials needs to be understood and optimized in order to eliminate delamination caused by flux interaction during the ball-attach process or subsequent cleaning or reflow processes.”
As Andy put it so well, “The product that was good yesterday may not be applicable today,” and it’s the job of Andy and his Indium Corporation colleagues to keep ahead of the materials science curve, not just to keep up with a turning world, but to actually change it, for the better.
From Pittsburgh, PA, thanks for reading.
~PFW