Working from the mantra “None of us knows as much as all of us,” SEMI invited manufacturers of electronic components and systems to come together and discuss how to build smarter fabs and reap key benefits like lower cost, faster turnaround as well as higher quality and more reliable products. The second annual Smart Manufacturing Workshop, held September 12, provided a very sensible approach to making our fabs more productive, The four sessions focused on four key topics:
- Current and future manufacturing solutions, chaired by John Behnke, INFICON /FPS
- Gaining trust in data security and sharing, chaired by Robert Albach, Cisco
- Blueprint for data flow architecture, chaired by Krish Dharma, IBM
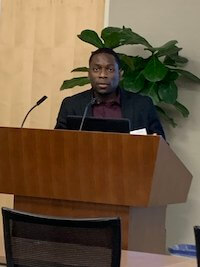
SEMI’s Ayo Kajopaiye, in his role as Project Coordinator of Collaborative Technology Platforms, organized and managed the event well (Figure 1). He’ll summarize it, and share the findings with SEMI members and use key topics as starting points for future workshops.
The workshop started with a brief introduction by Kajopaiye and Stephanie Harvey’s outline of FlexTech’s public/private consortium model.
Keynoter Kirk Wheeler, Staff R&D Engineer/Technologist at Intel, explained it best: Smart manufacturing is all about time. After instantly capturing and analyzing data, management needs to take appropriate actions in real-time. This message became the backbone of the entire workshop.
Wheeler provided clear examples of why a high-volume manufacturing facility demands close monitoring of specifications and, if deviations occur, immediate action. He strongly suggested that operations management needs to learn from every problem so that they can react even faster to similar situations in the future.
Each session, chaired by an industry veteran, included two manufacturing experts presenting how their company is addressing the specific topic or how their company can assist customers to solve it. Then individual groups discussed the session topics further and shared their findings/suggestions with the entire audience. It was a very engaging model to run a workshop.
Current and future manufacturing solutions
Manuel Aybar, Manager of Industrial Engineering at Qorvo, talked about how to transform a legacy manufacturing facility into a leading-edge factory. He shared how to prepare an ROI analysis, get top management support and deploy the approved funds wisely.
Azad Jafari, Senior System Engineer at Siemens, looked back to 1847 when 10 people started Siemens in Berlin. He described Siemens’ major steps: electrification, automation, and digitalization that took Siemens to today’s $83 Billion annual revenue. He discouraged relying on home-grown factory management systems and recommended ANSI/ISA95 reference factory architectures and reputable development partners – like Siemens. Jafari said the five stages to building a state-of-the-art factory are factory design, production planning, product engineering, product execution, and complimentary services.
Gaining trust in data security/sharing
Brian Hill, Manufacturing Project Manager at Itron, explained how to assure data security in electronic manufacturing services (EMS) environments. He addressed the common difficulties companies experience when data sharing is needed to debug yield problems, reduce lead-times, and improve quality.
Cisco’s Nancy Cam-Winget, Distinguished Engineer, talked about best practices and standards for data security and sharing.
During lunch, Puskar Apte updated us on SEMI’s Smart Manufacturing Benchmarking Survey and outlined the organization’s strategic cooperation with Cornell University’s Nanofabrication facility. This project will generate an open-source artificial intelligence/machine learning (AI/ML) framework for semiconductor manufacturing and propose standards for data formats and secure data transfer methods. Apte encouraged us to join the Industry Advisory Committee for this program.
A blueprint for a data flow architecture
Best practices for implementation of a digital architecture for a smart factory was the topic of IBM’s Masahide Hirouchi’s talk. He is a senior architect for semiconductor manufacturing solutions. He explained that especially countries with a shrinking workforce (like Japan) need automation to boost output. Then he outlined the path from a legacy to a smart, then to a cognitive factory and emphasized that IC fabs are the first factories to become highly automated. He predicted that other industries will follow soon. Like other speakers, Hirouchi also recommended we rely on a reference architecture for building the enterprise layer – factory – manufacturing – equipment – and physical layer for a state-of-the-art facility. Last, but not least, he praised digital twins.
Doug Suerich represented the PeerGroup, a major sponsor of this workshop. His talk focused on next-gen communication needs for smart manufacturing. While most of the workshop focused on wafer-fab topics, Suerich showed a slide from PDF Solutions that compared wafer fab and IC assembly challenges. The key difference between front-end (wafers) and back-end (packaging) are the manufacturing materials. Wafer fabrication uses a homogeneous material, while packages comprise heterogeneous materials. Another difference is that in the back end, carriers aren’t (or can’t be) standardized.
Communication between package manufacturing stages and product traceability are still limited. Suerich highlighted that back-end factories are getting more and more complicated to build and run. Like previous speakers, he explained why a smart factory needs to capture tons of data and have high-speed links to feed it to computers for analysis. While current factories use both wired and WiFi data transmission, Suerich noted that BOSCH is currently building a “5G only” factory.
Digital building blocks: AI and ML
Craig Hall, Director Process Engineering at Qorvo in Texas, showed how many different substrates (GaN, SOI, SiGe, RF SAW, …) Qorvo uses to serve high-speed applications. He explained how his team uses algorithms for automating trial and error routines to increase yields. Hall emphasized that customers demand increasingly complex solutions from semiconductor vendors (e.g. multi-function modules, 3D-ICs) which require multi-disciplinary engineers to design, manufacture, and test.
Joe Lee, Senior Product Marketing Manager at BisTel addressed how AI can drive trace analytics, provide decision support for humans, accelerate decision making and help bridging the widening gap between increasing amounts of sensor data and shrinking numbers of experienced human resources.
When the discussion group leaders summarized the findings of all four sessions, it became clear that factories need 5G for internal and external communication. Likewise, expanding from the current 1000 manufacturing standards SEMI already established, is mandatory.

While some innovations benefit wafer-fabs and assembly stages, back-end facilities require many additional and different measures. Everybody agreed that modeling to fully utilize digital twins is important, but still in its infancy. Many have high hopes that augmented reality will improve manufacturing and operator training. Last, but certainly not least, all expect that AI and ML will trigger major changes and make manufacturing faster, more cost-effective and help to save energy.
This workshop focused mostly on infrastructure and equipment topics. The Strategic Materials Conference (SMC 2019) at the DoubleTree in San Jose, on September 23 to 25, will give you in-depth information about materials innovations and their role in smart design and manufacturing environments.
For the latest about how AI and ML contribute to IC and System design and simplify manufacturing, please join us at the Electronic Design Process Symposium at SEMI in Milpitas, on October 3 and 4.
Thanks for reading….Herb