The world wants intelligence in everything, especially things that aren’t nailed down like autonomous cars, and the internet of things (IoT) devices. And suddenly, semiconductors are the hottest game in town. Here’s how some of these trends are impacting suppliers that I spoke with at SEMICON West.
The importance of purity
While Entegris is agnostic to megatrends, Jim O’Neill, CTO, still pays attention, and he says they all point in the same direction: to high-end logic, more standard logic, more memory, faster busses. “This means 3D integration and wafer level packaging,” he said.
And because of end-use applications like ADAS systems, the reliability of components is more important than ever. A direct line can be drawn from the purity of materials used to build semiconductor devices to device reliability. This is good news for Entegris because the company specializes in materials enablement with products for filtration, purification, materials handling, delivery and dispense.
It’s important to understand how materials impact the silicon from the growth of the ingot all the way through device dicing. “What adds value to the device is the performance materials leave behind. What adds value to the materials is the purity and quality,” explained O’Neill. “Customers aren’t just looking for a supplier that can manufacture clean chemicals, they want to ensure the integrity of materials across the system.”
OEMS as customers
Kamel Ait-Mahiout, the new CEO of Unity Semiconductor, also offered an interesting perspective on the impact of automotive electronics. “Silicon technology in the car is the same that’s used in the mobile phone, but it has to be more reliable,” he explained. The electrification is different, the substrate is changing, and it’s important to have the right tool that can inspect these.” Because of the increase in electronic content, automotive OEMS are becoming direct customers and driving reference designs.
This is driving Unity’s new business strategy, said Ait Mahiout. With tools focused on process control for photonics, 2.5D, and 3D applications, the company is shifting away from being “an engineering company” driven by the market, to one who’s experts solve customer solutions. This approach allows them to collaborate directly with the OEM and help them learn what they need, creating value.
After acquiring German-based HSEB earlier this year to expand its inspection tool portfolio, Unity has opened divisions in the US and Taiwan to put its experts directly where they need to be, rather than rely on sales reps in those regions.
Volumes matter
How do equipment manufacturers measure success? According to Veeco’s Rezwan Lateef, it’s by the volumes. The more volumes needed, the more tools are sold. That’s why when there was a large expansion in the mobile space, equipment suppliers did well.
Nowadays, the variety of applications call for a variety of different package types, including fan-out (FO), 2.5D, 3D, systems-in package, and more. Lateef explained that this diversity in package types makes it more difficult to become cost efficient with volumes.
In the world of lithography for advanced packaging, and particularly high-density fan-out (HDFO), Veeco is trying to push the envelope to help the industry grow. I/O density is driving advanced packaging to where it hasn’t gone before. Lateef says the increase in HDFO, either stacked or planar, is requiring sub 1µm line/space resolution, and Veeco lithography tools are ready to support that.
“There are many applications being developed that we can address,” said Lateef, “Which of these FO implementations succeed and can be tied to a volume source is what allows us to expand our business.”
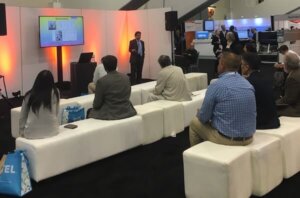
Smart manufacturing means actionable data
Smart manufacturing is so big, there was an entire pavilion dedicated to it at SEMICON West. According to Tim Kryman, advancements in artificial intelligence (AI) and machine learning (ML) have enabled a big shift in Rudolph Technologies’ approach to its yield management software. Its systems have always collected the data at metrology points to find the defects, but now they are able to analyze the data and understand how it connects to each other.
For Rudolph, “smart manufacturing” means making data more actionable, and connecting its yield management capabilities across not only its own tools but multiple tools across multiple fabs around the world.
Kryman says this is what sets Rudolph’s software apart from its competitors. “We can trace excursions in the die all the way through the manufacturing process,” he said. “That way we can find the defect, tell you where it happened, why it happened, its depth location, and who was running the tool at the time.” That’s powerful stuff.
Find more SEMICON West conversations about ML, AI, and its impact on the industry here. ~ FvT